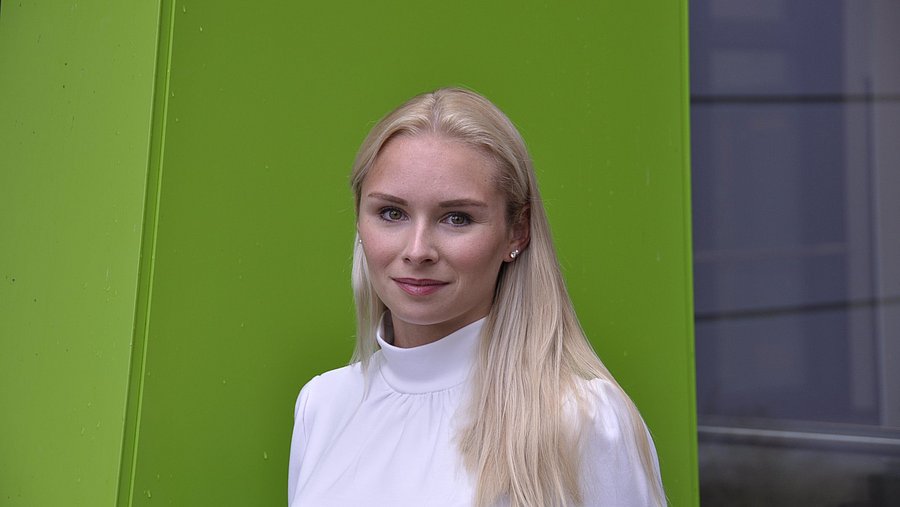
For a sustainable future in the metal industry
Leandra Apolte / Team Third Mission, bergisch. kompetenz project
Photo: UniService Third Mission
For a sustainable future in the metal industry
Leandra Apolte on the educational and scientific programmes offered by the bergisch.kompetenz project for SMEs
The University of Wuppertal is always interested in close co-operation with the Bergisch economy. In the past, it has repeatedly organised projects to this end. The bergisch. kompetenz project has now been running for over a year, funded by the European Regional Development Fund by the Ministry for the Environment, Nature Conservation and Transport of the State of North Rhine-Westphalia with a project duration until 2027. What is it about?
Leandra Apolte: The bergisch kompetenz project supports manufacturing companies in the metal industry in actively shaping a sustainable future. Innovative training programmes are aimed at small and medium-sized enterprises (SMEs) in particular, both at management level and especially at production level, in order to realise the transition from a linear to a circular economy.
The competence centre works with innovative approaches from business psychology and labour research. Experts from the fields of circular economy, production technology, education and regional transformation work closely with industry. The aim is to establish a centrally coordinated but decentrally organised centre of excellence at three regional locations: Wuppertal is mainly concerned with educational innovation, management development and start-ups, Solingen deals with manufacturing technologies and industrial design and Remscheid is responsible for technology, process design and simulation.
The project is being supported from various scientific perspectives. So, what are these perspectives?
Leandra Apolte: As the central topic is the development of skills, Prof Stefan Diestel’s Chair of Work, Organisational and Business Psychology is involved, which is contributing to the development of interactive and practice-oriented learning opportunities with gamification elements such as business games or escape rooms. At the same time, of course, technical expertise is also needed, especially when you enter into a discussion with the metal industry. This is why Prof Arne Röttger, Head of the Chair of New Manufacturing Technologies and Materials, and Dr Tim Katzwinkel’s Institute for Product Innovation are also part of the project. Together, they are looking after the technical processes that are to be designed to be resource-efficient.
Which other partners are you working with in this project?
Leandra Apolte: Neue Effizienz is in charge of the project. Other partners include the Collaborating Centre on Sustainable Consumption and Production (CSCP), the Wuppertal Institute, Fraunhofer UMSICHT, the FGW Research Association for Tools and Materials e.V., the Technische Akademie Wuppertal e.V. and Beck und Consorten, all of whom are working on the project at a scientific, strategic and political level. And, of course, our companies.
bergisch. kompetenz aims to put the regional economy in the fast lane. What is your role in this?
Leandra Apolte: I’m primarily responsible for internal tasks at the university. My goal is to work with various departments and professors to develop a sustainability-oriented master’s degree programme that enables students to take an in-depth look at the topic of sustainability and thus also the circular economy. Collaborating with companies from the region is particularly important to me and benefits both sides: The students work on real issues from practice and develop scientifically sound solutions, while the companies gain new perspectives and, in the best case, specific approaches to solutions.
Why not let industry do this alone, i.e., why bring the university to the table?
Leandra Apolte: Switching to a circular economy is a far-reaching transformation process that affects all levels of a company - technically, organisationally and culturally. Small and medium-sized companies in particular often lack the necessary knowledge and human resources to systematically tackle such processes. The university provides scientifically sound methods, models, and tools - especially for developing expertise at the three levels mentioned - and thus creates a structured basis for sustainable change.
One approach is a module designed at the university in mechanical engineering under the direction of Prof Arne Röttger entitled “Materials science and sustainable development”. What is this module about?
Leandra Apolte: The bergisch. Kompetenz-Contest was launched as part of the “Materials Science and Sustainable Development” module, a compulsory module in the master’s degree programme in Mechanical Engineering. The students develop technical solutions for specific problems from our partner companies, meaning that our partner companies approach the mechanical engineering department with problems and the students work on solutions. They also get in touch with the companies in order to scrutinise processes and deliver potential solutions directly back to them using the strategies they have learned in the subject area for resource-saving handling of products.
The teams use the CES-Granta Design software to select suitable materials and carry out an ECO audit, so factors such as raw material consumption, energy requirements during use, disposal and production, CO2 carbon footprint, water consumption, etc. are analysed. This systematic assessment of the environmental impact of a product, so to speak, enables them to subsequently implement their concepts as prototypes.
The special thing about this approach is that the students work on really urgent questions from the business partners. Which business partners are taking part in this project?
Leandra Apolte: This is correct - the students receive tasks of companies located in the region. For example, Freund, a manufacturer of tools for roofers, is developing sustainable solutions for forming sheet metal. Muckenhaupt & Nusselt, a cable manufacturer, is looking for ways to reuse production waste from sheathing in manufacturing and Bauer & Böcker, a company from the magnet, LED and laser technology sector, is looking at how industrial lighting can be made even more sustainable.
Other industrial partners are, of course, always welcome. We are always happy to receive enquiries from industry.
A new feature of this project is a kind of competition, which will also lead to a presentation on 9 July, even a prize is awarded. What happens there?
Leandra Apolte: On 9 July, the students will present their solutions in a pitch to a jury made up of representatives from the participating companies, Prof Röttger, Neue Effizienz and myself.
For the students - many of whom are about to graduate - this competition is an excellent opportunity to gain practical experience in dealing with companies, beyond traditional job application situations.
The best solution will be honoured with the bergisch. kompetenz Löwe - a kind of trophy for sustainable innovation. The results will then be presented to a wider public in due course.
What happens after the competition?
Leandra Apolte: My wish is that we can realise even more such collaborations in the future - with more companies, new modules, and more students. After all, it is precisely this exchange between science and business that harbours the great potential to shape real transformation in a sustainable and practical way. The collaborations could grow and we could expand our master’s programme accordingly, which would be a win-win situation for both sides.
Uwe Blass
Leandra Apolte is a research assistant at the Department of Design at the School of Mechanical Engineering and Safety Engineering. In the bergisch. kompetenz project, she is working with departments and professors on a sustainability-oriented master’s programme as part of the UniService Third Mission.